IVITAS, a.s.
IVITAS started operations in 1996, when it opened its design office in Ostrava.
We provide our clients with design, construction and consulting services in the areas of energy, metallurgy, ecology and technological installations for buildings. We focus on steam and hot water boilers, electric power plant boilers, heating plants and industrial facilities.
Our experts carry out the supervision and optimization of operations. We work with modern software tools for calculating and designing in 2D and 3D spaces. Our team is ready to work with any level of documentation - from studies to workshop documentation. One of the strengths of our company is our team of experienced professionals from various fields – computing specialists, designers and engineers. This well of talent allows us to provide our clients with comprehensive solutions.
IVITAS is certified under ISO 9001:2015 and ISO 27001:2022.
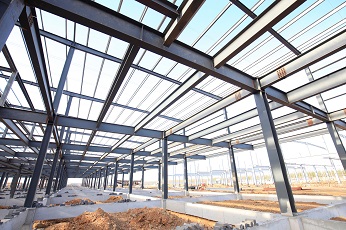